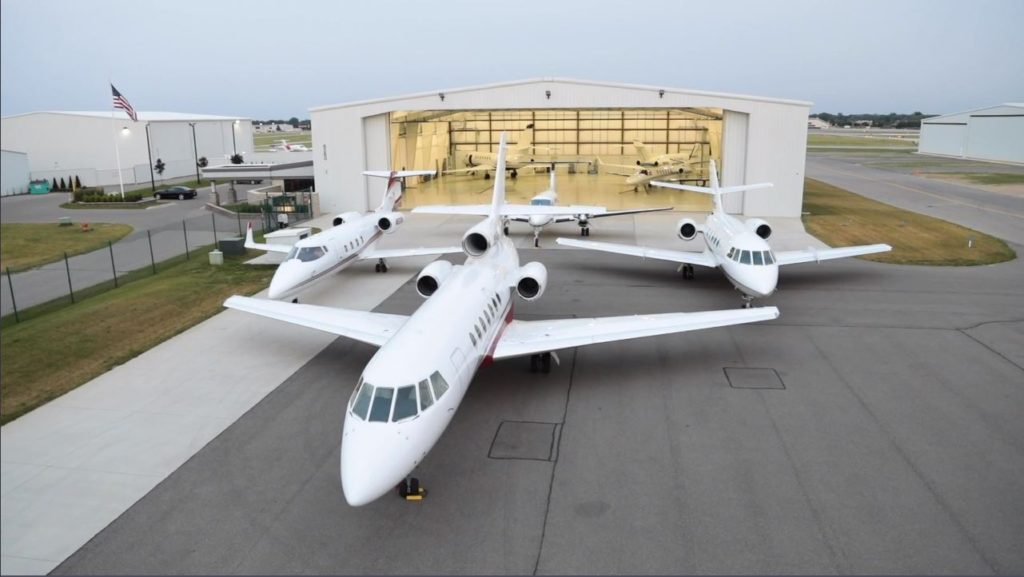
Process of Buying a Steel Building
History
The steel building industry has evolved at an incredible rate in a very short period of time. Everywhere you look, steel buildings are being constructed. Pre-engineered steel buildings are replacing conventional wood/masonry structures in every segment of the construction industry. As the construction community continues to evolve, the steel building industry continues to meet the challenges and make the necessary technological changes that allow pre-engineered steel to be the preferred choice for construction materials.
At American Steel Buildings, LLC., it is our desire to combine the best product for the best price and provide the best customer service that is available in America and around the World. Our goal is to become the World’s leading provider of steel buildings and metal components. From factory buildings to churches, our technology and engineering capabilities allow us to create structures that:
- Exceed standard loading or size requirements
- Are designed to meet your specific needs
- Cost up to 39% less than traditional construction methods
- Allow for easy expansion in the future
- Reduce energy costs
Know what you need
Before you even contact a supplier, make sure that you know what you need. For example, what size of a building is actually going to fit on your property? What type of property setback, if any, does your county require? What items do you need and what items do you want? When contacting a company, one of the first questions asked will be what size of building are you looking for? When this question is asked, it is not a question regarding square footage. What the supplier needs are the dimensions of the building. The most common dimensions are given in Width ___ Length ___ Eave Height ___ and Roof Slope ___ . The width of the building is the Gable End. The Gable End of the building is most commonly described as the end that resembles an “A”. The ridge of the building will run the “length” of the building. The “eave height” is the outside wall height, where the walls meet the roof. It is very important that one doesn’t get the width and length confused, as this will typically affect the price of the building.
Make sure that if there are any critical interior dimensions, you make the supplier aware of them. For example, you may need an interior clearance of 10′ high, but you only request an outside eave height of 12′. Depending on the width of the building, and some other factors, the actual interior clearance on a building with a 12′ eave height might be more around 9’6″. Without you advising the supplier that this was critical, this might not be caught until the drawings are issued. Once drawings are issued, any major changes to the building are very costly. This is because all the engineering work that was previously done will now be void and the building must be re-designed. This also applies to any width or length dimensions that are given.
Another point that must be expressed is what you intend to do with the outside of the building. There are many times that the customer may want to apply something other than steel to the exterior. When this is the case, it is very important that the supplier knows this in the beginning so that the correct design material can be quoted. One example of this is if there will be block on any part of the building. If the block is going to be 8′ then supplier must set the columns in a “by-pass” condition so that the outside steel line will be in line with the outside face of the block. A special base angle or base channel, with base flashing must also be included so that the steel can be “tied-in” correctly to the block.
One of the best ways to describe exactly what you need is to draw a picture. Even the most basic and rough picture will be helpful to the supplier as they try and visualize what you are envisioning. If you feel as though you cannot draw a picture accurately, ask the supplier to draw a basic sketch of what the two of you have discussed, and see if they are on the right track. This will allow you to become more comfortable with whomever you are working with, and also know that what is being quoted is the correct design.
Choose a supplier
Choosing a steel building supplier is much like purchasing anything else. First, you must educate yourself and know what you are buying. Too many times customers get “taken” and buy into a story instead of sticking to what they know they need. Remember, you are buying a building, not a car. Unlike cars, there are not lots that are full of buildings that have been fabricated, and are just waiting for someone to come along and find exactly what they need. There is the exception when a building has been fabricated, and for one reason or another, the customer was unable to pay for and accept the building. As you read on, you will see why this does not happen very often.
Second, and probably the most important, contact no more than three suppliers. If you contact more than three suppliers, it can sometimes be too confusing. The easiest way to contact multiple suppliers is to search the Internet. Once you contact a building company, make sure that they are listening to your needs, not telling you what they think you need. Make sure that you feel comfortable with whomever you are speaking. Find out if the person you are presently speaking with is the same person that you will speak with from the time an order is placed until the building is delivered. This ensures accountability between you and the representative. Some companies have a sales department, and then once the sale is complete, the order is turned over to another department. This can sometimes be very frustrating, especially if you do not know who you need to talk with if a change is needed. Another great way to maintain accountability is to keep a paper trail. Make sure that whenever something important has occurred, have it documented, and signed by both parties. This is very important so that you never get into a “he said, she said” battle.
Never make a quick decision and be sure that you know exactly what you are buying. Do not assume anything! What can be misunderstood usually will be misunderstood. Remember that communication is the best way to establish a relationship and to build trust. While price matters, it is not the most important factor when making your final decision. You will want to make sure that whatever quotes you are comparing, match up “apples for apples”. If one manufacturer verbally tells you that something will be included, but you do not see it on paper, have them verify it in writing. The manufacturer should have no problem with this if it is actually intended to be included. Verify the shipping weight of the building. Many manufacturers do not initially give this information, however, it is very important when comparing quotations. If two quotes are close in price, but are considerably different in weight, that is something that you will want to consider with your decision. The weight of building lets you know the quality of the steel, and the “beefiness” of the building.
Another factor, and this ties into why you will not find buildings laying around in a lot waiting to be purchased, is what building code / loads are being quoted. Each state has a specific building code that your building must be certified for when obtaining permits. More specifically, each county in that state will have specific loads that you must conform to, otherwise you will not be issued your permit to occupy your structure. The loads of importance are the Live Load, the Snow Load, and the Wind Load. The Live Load is defined as “Loads that are produced (1) during maintenance by workers, equipment, and materials and (2) during the life of the structure by movable objects but does not include wind, snow, seismic or dead loads”. The Snow Load is defined as “The vertical load induced by the weight of snow, assumed to act on the horizontal projection on the roof of the structure”. And lastly the Wind Load is defined as “The load caused by the wind from any horizontal direction”. Another load that is important, and must be addressed is Collateral Loads. Collateral loads are defined as “The weight of permanent materials other than the building system, such as sprinklers, mechanical systems, electrical systems, partitions, and ceilings”. Collateral Loads are not always required, however, with all load information, you must make sure that you contact your local building department to verify what is required. Even if you have multiple quotations that all have the same loads being quoted, it is the customer’s responsibility to verify the correct information with their building department. Make sure that you obtain the name and phone number of whomever you speak to, and make sure that they are an actual inspector and not an office clerk/secretary…
Process of ordering and time
The process of ordering a building is very simple. Once the quotation has been accepted, and the customer is ready to sign the contract, there are two payment options that are normally offered. The first is the most common, and is the safest way to proceed. A Permit Drawing deposit, usually 10% (but not less than $1,500.00) is required in order to process the pre-engineered drawings. The engineered drawings will take anywhere from 2-1/2 to 3 working weeks depending on the complexity of the project. Once the drawings are received, it is the customer’s responsibility to take the drawings to their county, and obtain the necessary building permits. Once the permits are obtained, and the drawings have been reviewed and accepted, it is now time to place the building into the fabrication schedule. Typically, a 25% deposit will be required at this time. Production will take anywhere from 6 to 8 working weeks. This can sometimes be as short as 4 weeks, and could be as long as 10 to 12 weeks depending once again on the complexity of the project. If there are any changes that need to be made, the time to do this is before you place the building into production. If fabrication of any part of the building takes place, and then a change is required, the customer will not only be charged for the change, but also any part that may have already been fabricated. Throughout the entire ordering process, make sure that you once again keep a paper trail of everything that takes place. For instance, if any changes take place, we will issue what is called a “change order”. The change order will explain what is being changed, and what type of affect it will have on the price. In order for the change order to go into effect, it will be required to be signed and returned so that nothing is changed without the customer’s approval. Also, after every money transaction, an invoice/ receipt will be submitted so that there will be no misunderstandings at the time of delivery. At the time of the delivery, a COD Cashier’s Check will be presented to the driver of the truck. Once the check is presented, the driver will then allow the customer to begin to unload the building.
Delivery
At delivery of each building, a complete Bill of Lading will accompany the building materials. The Bill of Lading will list every building part that comes with your building. Each part will have a “piece mark” that will correspond with the (3) three sets of construction drawings that will also be included at delivery with your building materials. The customer or his construction representative will be responsible for unloading his building from the truck. At this time, the customer will be able to use the Bill of Lading to do a complete inventory. Once the building materials have been unloaded and the inventory is finished, if there are any items missing or damaged, the customer or his representative will contact our office at (800)-511-3670. Even though we take load photos and carefully check each truckload, there is always a chance for human error. However, we will work together with our Customer Service Department and the customer or his representative to replace these items as promptly as possible.
What to expect after delivery
During the construction phase of the project, if there happens to be a part of the building that has been fabricated wrong, the customer or his representative will follow these procedures:
- Contact our office immediately with a complete description of the problem with part number and its location on the construction drawings.
- Our Customer Service department will document the problem, review the piece that is in question, and will advise the quickest solution to overcome the problem.
- Once the problem has been documented with Customer Service and it has been verified as to what must be done to correct the problem, the owner or his representative will submit a detailed bill/back charge showing what work was performed. This bill/back charge will give the number of hours and the price per hour it cost to make the corrections.
- Customer Service will then review the billing, contact the owner or his representative with any questions, and finally issue the agreed amount to the owner or his representative.